Overview:
Coca-Cola’s Flight Department sought to address several challenges with its traditional Maintenance Risk Assessment Tools (MRAT), which had become inefficient and unreliable. These issues included inconsistent assessments, poor mitigation adherence, and missed critical safety information. Led by Brad Johnson, Aircraft Program Manager, Coca-Cola decided to tackle these challenges by implementing Polaris Aero’s GroundRisk, an advanced risk assessment system integrated into their existing VOCUS Safety Management System (SMS), offering a more objective and streamlined approach to hazard identification and mitigation.
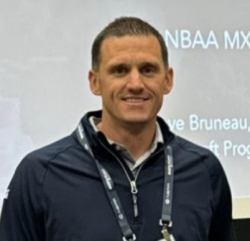
Challenges with Traditional MRAT:
“We have a great group of technicians but lacked some structure that could help us be more process-driven and scalable in our safety approach,” said Johnson.
Some of the challenges were:
- Inconsistent Usage: MRATs were not consistently performed, often skipped or filled out quickly without a thorough review.
- Lack of Customization: The MRAT used the same set of generic questions for all tasks without adjusting for specific operations or company SOPs.
- Human Error & Subjectivity: Technicians perform the MRAT subjectively; depending on their experience, the results could lead to inaccurate risk assessments and unaddressed hazards.
- Failure to Capture Lessons Learned: Important insights from past incidents were frequently forgotten, leading to repeated mistakes and safety events.
- Low Engagement: Over time, MRATs became a chore, with little perceived safety value, causing employees to disengage from the process.
Implications:
The traditional MRAT’s limitations led to underestimating or missing critical hazards, potentially resulting in safety incidents. The lack of accurate assessments impacted staffing decisions, operational efficiency, and safety.
Solution:
Coca-Cola implemented GroundRisk, an advanced risk assessment tool that automates the hazard identification process based on published rules, regulations, and company procedures.
Unlike subjective MRATs, GroundRisk:
- Pulls data from the maintenance schedule and integrates it with company rules, flagging relevant hazards.
- Provides a more objective and consistent way to assess risks, reducing the potential for human error.
- Offers automated recommendations for mitigating risks and improving maintenance operations' safety and efficiency.
Key Features of GroundRisk:
- Automated Hazard Identification: Using a rules engine, GroundRisk analyzes scheduled tasks to identify relevant hazards and suggests mitigation actions.
- Customizable to Company SOPs: The tool allows Coca-Cola to input company-specific rules and procedures, ensuring compliance and consistency.
- Data-Driven Scheduling: GroundRisk’s work schedule offers visibility into staffing levels and workload, allowing for better resource planning.
Impact:
“While we’re still new to GroundRisk, the early gains are starting to show,” said Johnson. “The transparency of information along with the increase in codifying our lessons learned in GroundRisk will only continue to improve our department,” said Johnson.
Some of the specific impacts that Coca-Cola has realized are:
1. Improved Risk Management:
- The calendar feature provides a clear overview of the work schedule, allowing managers to assess staffing levels and ensure proper coverage ahead of time. For example, when a nighttime aircraft launch was identified as understaffed, the team could reallocate resources in advance, avoiding last-minute scrambling.
- This proactive approach helped ensure all tasks were completed on time and with the appropriate safety protocols, enhancing overall operational efficiency.
2. Better Compliance with SOPs:
- Coca-Cola customized GroundRisk to include reminders based on their specific Standard Operating Procedures (SOPs). For instance, the Engine Run rule ensures that technicians are certified and work is signed off before performing engine tests.
- Other procedural rules, like those for Single Point Refueling O-Ring Replacement and Duty Day regulations, help maintain safety while aligning with company practices, ensuring all technicians know the steps required for safe operations.
3. Enhanced Collaboration Across Shifts:
- GroundRisk has improved the handoff of tasks between shifts and technicians. Technicians can pause tasks and hand them off seamlessly to another technician, ensuring continuity and that no safety steps are missed.
- This has been especially useful in aircraft launches, where one technician may handle the preflight checks, and two other techs handle the fueling and final preparations.
4. Operational Efficiency:
- GroundRisk has allowed Coca-Cola to better plan and manage its workforce, including contractors and FAST teams. By seeing staffing availability ahead of time, the team can make informed decisions about engaging outside resources, ensuring tasks are adequately staffed without unnecessary delays or stress.
Key Takeaways:
- Early Hazard Identification: Automating the risk assessment process has allowed Coca-Cola’s Flight Department to spot and mitigate potential hazards earlier, leading to safer operations.
- Team Collaboration: Proactive planning and schedule visibility have enhanced teamwork and ensured the right resources are available.
- Increased Safety & Efficiency: By integrating GroundRisk with their SMS, Coca-Cola has achieved better hangar risk management, reduced reliance on memory, and improved overall operational effectiveness.
- Customization & Compliance: Tailoring the tool to their specific needs and SOPs has increased compliance and provided critical reminders for technicians, reinforcing safety at every step.
Conclusion:
“By adopting GroundRisk, our Flight Department is transitioning into a more effective, risk-managed, and data-driven approach, which will help us achieve our goals and meet the mission of our core business customers,” said Johnson. “This shift has not only improved safety outcomes but also enhanced operational planning, reduced staffing issues, and fostered a more collaborative work environment,” said Johnson.
GroundRisk has proven invaluable in managing hangar operations and ensuring the department operates at peak safety and efficiency.